ELECTROSTATIC OILERS
Terronics electrostatic oilers provide a better way to oil strip materials for rust protection or lubrication.
Most existing methods are ineffective and cause oil handling headaches. Mechanical methods of oil deposition (rolling, dripping, pumping, blade wiping) as well as most semi-electrostatic methods are imprecise and require over-oiling to ensure total strip coverage. This leads to high costs of oil removal, disposal coil handling problems and safety/housekeeping problems from runoff of excess applied oil both for you and your customers.
​
​TDC's electrostatic oilers deliver the most uniform targeting and control of oiling possible. Strip coverage is uniform and typically controllable within +/-10mg/ft sq. With this degree of uniformity, 50mg oil/ft2 (or less) is sufficient to provide complete coverage against rusting.

ELECTROSTATIC OILER BENEFITS
Preserve Product Quality
Precise targeting provides total strip coverage.
​​​​​​​
​​
​
Improves Coil Handling
Reduces telescoping of coils.
​​​​​​​​​
​
​
Improves Safety and Housekeeping
Precise targeting and control eliminate overspray and reduce hazard and mess of oil runoff from coils, both for rolling mills and their customers.
Minimizes Oil Usages
Can reduce oil usage to as little as one-fifth of currently applied levels.
​​​​​​​
​
Reduces Customer Oil Disposal Problems
Less oil applied means that your customers pay less to remove and dispose of oil.
​
​
Allows Flexible Processing
A wide range of strip widths can be processed on one machine. Oil application is possible from both top-down and bottom-up orientation.

What Makes
TDC Unique?
Controllable
Reliable
Uniform
Efficient
Understanding Electrostatic Oilers
Electrostatics is the science interested in beneficially harnessing the many characteristics of electrostatic forces. The fundamental principle is based on mutual attraction of opposite electrical charges and mutual repulsion of like charges.
TDC's focus of applied electrostatics looks for creative ways to safely and effectively charge particles (liquid droplets or solid particles) so that they are attracted to intended targets and provide a high quality coating.
​
The principle behind this physics was applied first in the early 1900's in electrostatic precipitators to remove dust particles from smokestacks. Later it inspired the development of electrophoresis, powder paint sprayers, xerography, separation of metallic ore from tailings, and ink jet printers. But this subtle, yet powerful physics is far more useful than even these widespread applications. From what we have discovered at TDC, we know it has vast, yet-undiscovered potential.
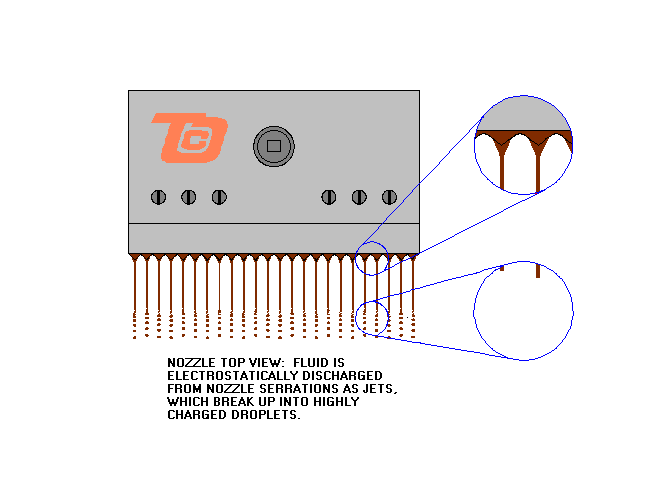
The Electrostatic Coating Process is Simple.
The target substrate is electrically grounded. The coating system creates electrical charges, and disperses particles or droplets toward the target by a variety of methods. The charged particles are attracted to the electrically grounded substrate and are deposited on it.
That's only HALF of the Story: the "Opposites Attract" Half
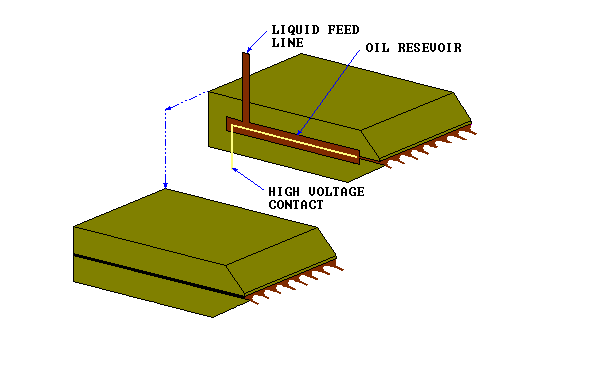
Like charges also repel. Since the charged particles are all charged alike they repel each other. During flight to the target and while "landing", particles avoid each other and seek areas on the target surface that are best grounded (i.e., uncoated areas).
This is the idea behind one of the many elegant aspects of electrostatic coating processes: deposition is uniform because the least coated areas get coated by the "newest" particles.
Of course there are some subtle arts to this science: fine atomizing of liquid droplets, fine deagglomerating and diffusion of powders, eliminating or shielding unintended targets, design and creation of an optimal electric field, optimizing equipment geometry and orientation, etc. But in solving these problems, and learning to harness the power of electrostatics, many useful material deposition processes become possible.
Electrostatics is a totally beneficial science.
Characteristics of well-designed electrostatic processes include:
-
low energy expenditure,
-
absence of pollution or other undesirable effluents,
-
and very high material utilization efficiencies.
Its applications reduce waste and improve manufacturing efficiency and product quality. There are no adverse secondary effects from application of electrostatics.
It is as efficient and basic to nature as the electron to proton attraction and as powerful as a bolt of lightning.
